Excitement About Additive Manufacturings
Wiki Article
About Manufacturing Industries
Table of ContentsAbout Manufacturing IndustriesEverything about Hon Hai PrecisionThe Best Strategy To Use For OemOem for DummiesSome Known Factual Statements About Plastic Manufacturing Indicators on Hon Hai Precision You Need To Know
The message on this page is a sample from our full White Paper 'Injection Moulding for Customers' - * Example message * - for full overview click the download switch over! Introduction This overview is intended for people who are looking to source plastic mouldings. It gives a much needed understanding right into all that is involved with creating plastic components, from the mould tool needed to the moulding procedure itself.If you desire to discover even more, the overview covers sorts of mould devices, as well as special completing processes such as colours & plating. Words that are underscored can be located in the reference in the appendix ... Component I: Moulding: The Essentials The Advantages of Shot Moulding Plastic shot moulding is a really precise process that provides numerous benefits over other plastic processing methods.
Precision is ideal for extremely complex components. You can hold this moulding in the palm of your hand and it has bosses, ribs, metal inserts, side cores and openings, made with a gliding shut off function in the mould tool.
Mfg Things To Know Before You Buy
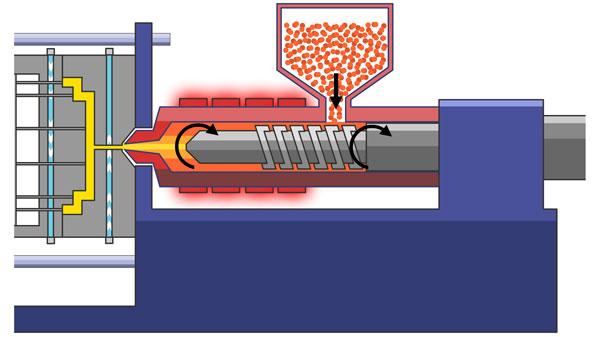

from product feed & melting; product shot; cooling down time and ejection to the re-closing of the mould device prepared for the following cycle. Draft angles - The wall surfaces of a moulded part must be slightly tapered in the direction in which the part is expelled from the mould tool, to enable the component to be ejected quickly.
Ejector stroke - The pressing out of ejector pins to eject the moulded component from the mould device. Ejector stroke rate, size and Read Full Article timing requires to be very carefully managed to stop damage to the ejectors and also mould device, however at the very same time make the moulding cycle as brief as feasible.
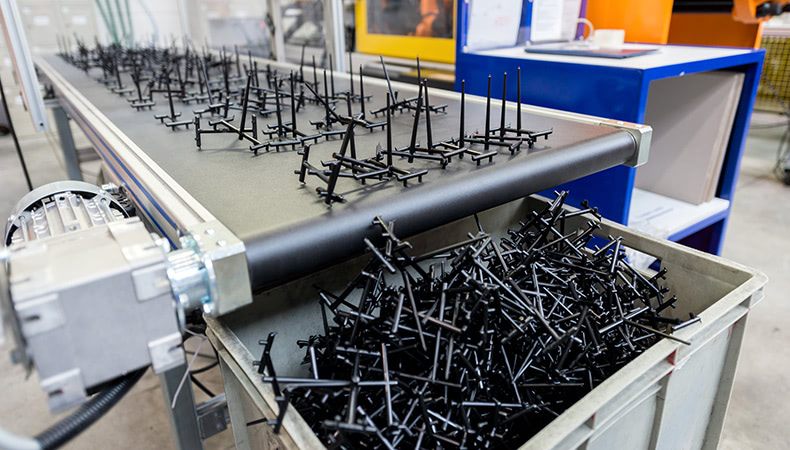
Get This Report about Additive Manufacturing
Ribs - When a plastic component has slim walls, ribs are included to the layout to make the slim wall surfaces stronger Side cores - Side activity which creates a function on a moulded component, at an opposing angle to the regular opening instructions of the mould device. additive manufacturing. The side core needs to be able to withdraw as the plastic component can Check This Out not be expelled otherwise.
Walls - The sides of a moulded component The text on this page is a sample from our full White Paper 'Shot Moulding for Buyers'.
Shot moulding is commonly made use of for making a variety of components, from the smallest parts to entire body panels of cars. Shot moulding utilizes a special-purpose device that has 3 components: the shot unit, the mould as well as the clamp.
Top Guidelines Of Lean Manufacturing
, with the quantity utilized of the former being substantially higher.: 13 Thermoplastics are common due to features that make them highly appropriate for injection moulding, such as simplicity of recycling, adaptability for a wide range of applications,: 89 and also capacity to soften and stream on heating.In multiple dental caries moulds, each tooth cavity can be similar and develop the exact same parts or can be distinct and form numerous various geometries throughout a solitary cycle.
The screw provides the raw product ahead, blends and homogenises the thermal and also viscous circulations of the polymer, as well as decreases the required heating time by mechanically shearing the product as well as including a significant amount of frictional heating to the polymer. The material feeds onward with a check shutoff as well as accumulates at the front of the screw right into a quantity referred to as a shot. When enough product has collected, the product is required at high pressure and rate right into the part developing dental caries. The specific amount of shrinkage is a feature of the resin being made use of, and also can be relatively foreseeable. To stop spikes in stress, the procedure normally uses a transfer placement representing a 9598% full cavity where the screw shifts from a constant speed to a consistent stress control.
A Biased View of Die Casting
Once the screw reaches the transfer setting the packing stress is used, which finishes mould dental filling and also makes up for thermal shrinking, which is rather high for thermoplastics about several various other materials. The packing pressure is applied till the gate (dental caries entry) solidifies. As a result of its little dimension, the gate is usually the starting point to solidify via its entire thickness.: 16 Once the gateway solidifies, no more product can go into the cavity; as necessary, the screw reciprocates and gets material for the next cycle while the material within the mould cools so that it can be expelled and be dimensionally steady.Report this wiki page